GD&T Interview Questions: A Comprehensive Guide to Ace Your Interview
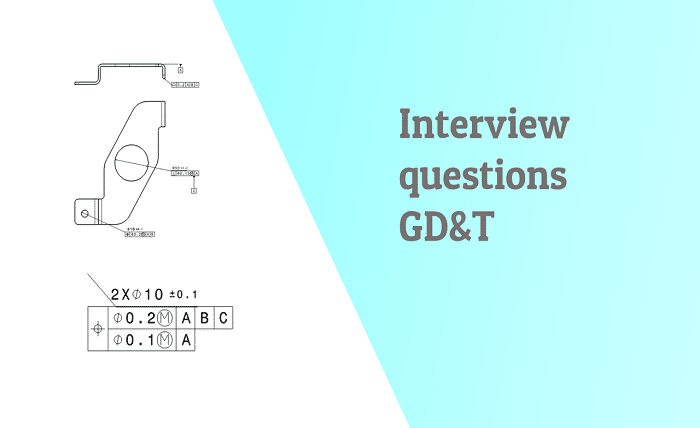
Are you preparing for an interview that involves GD&T (Geometric Dimensioning and Tolerancing)? To help you succeed, we have compiled a list of commonly asked GD&T interview questions and provided detailed answers. This article aims to equip you with the knowledge and confidence to excel in your GD&T interview. Whether you are a seasoned professional or a job seeker, this guide will assist you in understanding the essential concepts of GD&T and preparing for potential interview questions.
What is GD&T?
GD&T stands for Geometric Dimensioning and Tolerancing. It is a symbolic language used to communicate engineering specifications and tolerances on technical drawings. GD&T ensures that the manufactured parts meet the desired functional requirements by defining the allowable variations in form, size, orientation, and location.
Importance of GD&T in manufacturing
GD&T plays a vital role in manufacturing as it provides a precise and standardized method to define and control the variations in parts. It eliminates ambiguity and misinterpretation by specifying the allowable tolerances in a clear and concise manner. By using GD&T, manufacturers can enhance product quality, improve interchangeability, reduce costs, and ensure proper assembly and functionality.
Basic GD&T symbols and their meanings
GD&T symbols are graphical representations used to convey specific tolerancing requirements. Some of the basic symbols include:
- Feature Control Frame: This symbol contains information about the tolerance zone, geometric characteristic, and other control parameters.
- Position: Indicates the location of a feature relative to a reference.
- Concentricity: Specifies the center points or axes of two or more features that must be concentric.
- Parallelism: Ensures that two surfaces or axes are parallel to each other.
- Perpendicularity: Requires two surfaces or axes to be perpendicular.
- Circularity: Defines the tolerance zone for a perfect circle.
- Cylindricity: Specifies the tolerance zone for a perfect cylinder.
Types of tolerances in GD&T
In GD&T, there are several types of tolerances used to define the allowable variations in parts:
- Form tolerances: These tolerances control the shape, profile, and surface characteristics of features.
- Orientation tolerances: These tolerances define the allowable variations in the orientation of features such as perpendicularity, parallelism, and angularity.
- Location tolerances: These tolerances specify the allowable deviations in the position of features.
- Runout tolerances: These tolerances control the total variation of a feature as it rotates or moves along its axis.
Key benefits of using GD&T in engineering drawings
Implementing GD&T in engineering drawings offers several advantages, including:
- Ensuring clear communication and understanding of design intent.
- Reducing errors, rework, and manufacturing costs.
- Facilitating interchangeability and assembly of parts.
- Improving product quality and reliability.
- Enabling effective measurement and inspection.
- Enhancing the compatibility of parts from different suppliers.
Common GD&T Interview Questions and Answers
What is the purpose of GD&T?
GD&T serves the purpose of accurately defining the allowable variations in form, size, orientation, and location of features on technical drawings. It ensures that the manufactured parts meet the intended design requirements and can be assembled and function as intended.
Explain the difference between true position and position tolerance.
True position refers to the exact location of a feature relative to the specified datum reference. It is defined by both the location and the size of the tolerance zone. Position tolerance, on the other hand, specifies the allowable deviation from the true position. It defines the maximum permissible variation in position while ensuring proper assembly and functionality.
What are the basic principles of GD&T?
The basic principles of GD&T include:
- Ensuring clear and unambiguous communication of design requirements.
- Defining the allowable variations in form, size, orientation, and location.
- Establishing a datum reference frame for consistent measurement and inspection.
- Balancing the functional requirements with manufacturing feasibility.
- Facilitating interchangeability and assembly of parts.
How does GD&T improve product quality and manufacturing efficiency?
GD&T improves product quality by providing precise specifications and tolerances, reducing errors, and ensuring proper assembly and functionality. It enhances manufacturing efficiency by eliminating ambiguity, facilitating measurement and inspection, and enabling effective communication between design, engineering, and production teams.
What are the advantages of using GD&T over traditional dimensioning methods?
Using GD&T over traditional dimensioning methods offers several advantages, such as:
- Clearer and more concise communication of design intent.
- Enhanced product quality and reliability.
- Reduction in errors, rework, and manufacturing costs.
- Improved interchangeability and assembly of parts.
- Facilitation of effective measurement and inspection.
- Compatibility of parts from different suppliers.
Describe the Datum Reference Frame (DRF) and its significance in GD&T.
The Datum Reference Frame (DRF) is a three-dimensional coordinate system established by the datum features on a technical drawing. It serves as a reference for defining the position, orientation, and tolerances of other features. The DRF ensures consistent measurement and inspection across different parts and allows for accurate assessment of form, size, orientation, and location.
What is the difference between bilateral and unilateral tolerances?
In GD&T, bilateral tolerances allow variations on both sides of the nominal dimension, while unilateral tolerances allow variations only on one side. Bilateral tolerances are symmetrical, whereas unilateral tolerances are asymmetrical and can be used to control the direction of variation.
How do you interpret a GD&T callout on an engineering drawing?
To interpret a GD&T callout on an engineering drawing, you need to understand the symbols, modifiers, and control frames used. It is important to consider the geometric characteristic, tolerance value, reference features, and the specified datum reference frame. By analyzing these elements, you can determine the allowable variations and requirements for the specific feature.
Can you explain the concept of virtual condition in GD&T?
In GD&T, the virtual condition refers to the perfect or theoretical form, size, orientation, or location of a feature defined by its geometric tolerance. It represents the extreme limits of the part’s dimensional and positional variations while ensuring proper assembly and functionality. The virtual condition allows for accurate assessment of the part’s compliance with the specified tolerances.
Read more about:Â naz-tricks
What are the limitations of GD&T?
Some limitations of GD&T include:
- Complexity in interpretation and understanding for those unfamiliar with GD&T.
- Potential for miscommunication or misinterpretation if not properly documented.
- Need for skilled personnel and advanced measurement equipment for accurate assessment.
- Cost implications for implementing and inspecting GD&T requirements.
How does GD&T impact the manufacturing cost?
While implementing GD&T may initially require additional resources and expertise, it can ultimately lead to cost savings in manufacturing. GD&T helps reduce errors, rework, and scrap, resulting in improved productivity and efficiency. By providing precise specifications and tolerances, GD&T minimizes variation, enhances part interchangeability, and ensures proper assembly, reducing overall manufacturing costs.
Explain the concept of bonus tolerance in GD&T.
Bonus tolerance is an additional tolerance allowed beyond the specified tolerance in GD&T. It provides extra leeway to manufacturers without compromising the functionality or performance of the part. Bonus tolerance can be utilized when a feature’s actual condition is better than the virtual condition defined by the tolerance. It rewards good manufacturing practices and incentivizes process improvement.
How is profile tolerance different from position tolerance?
Profile tolerance controls the allowable variations of a feature’s entire surface or line in relation to the specified tolerance zone. It considers both form and location simultaneously. Position tolerance, on the other hand, defines the allowable deviation of a feature’s location from the true position. While profile tolerance evaluates the entire feature, position tolerance focuses on the feature’s location only.
What are some common applications of GD&T?
GD&T is widely used in various industries, including automotive, aerospace, manufacturing, and engineering. Some common applications include:
- Automotive part manufacturing and assembly.
- Aerospace component design and production.
- Mold and die manufacturing.
- Machining and fabrication processes.
- Quality control and inspection.
What are the challenges in implementing GD&T in a manufacturing process?
Implementing GD&T in a manufacturing process can present some challenges, including:
- Training and educating personnel about GD&T principles and interpretation.
- Ensuring consistent application of GD&T across design, engineering, and production teams.
- Aligning suppliers’ understanding and compliance with GD&T requirements.
- Maintaining proper documentation and communication of GD&T specifications.
- Acquiring and utilizing advanced measurement and inspection equipment.
Tips for Preparing for a GD&T Interview
To prepare for a GD&T interview, consider the following tips:
- Review and understand the fundamental principles of GD&T.
- Familiarize yourself with GD&T symbols and their meanings.
- Practice interpreting engineering drawings with GD&T callouts.
- Study common GD&T interview questions and prepare detailed answers.
- Take part in mock interviews or seek guidance from experienced professionals.
- Demonstrate your knowledge of practical applications of GD&T in manufacturing processes.
- Highlight your problem-solving skills and ability to apply GD&T concepts in real-world scenarios.
Conclusion
In conclusion, GD&T is a crucial aspect of engineering and manufacturing that ensures the accuracy, interchangeability, and functionality of parts. This comprehensive guide has provided you with an overview of GD&T, its importance, common symbols and tolerances, and answers to frequently asked interview questions. By thoroughly preparing for a GD&T interview and understanding the concepts discussed here, you will be well-equipped to impress potential employers and secure your desired position.